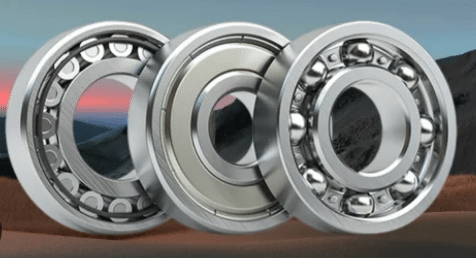
In the fast-evolving landscape of the bearing industry, digital transformation has become a key differentiator for companies like SKF and FAG. Embracing digital technologies and informationization processes has the potential to revolutionize product development, manufacturing, and customer service, ultimately impacting product quality and customer satisfaction. This article examines and compares the digital transformation journeys of SKF and FAG, shedding light on how their informationization processes influence product quality.
Digital Transformation Overview
1.1 SKF Bearings
SKF has been at the forefront of digital transformation, adopting innovative technologies to enhance various aspects of its operations. The company’s digitalization efforts encompass product design, manufacturing processes, supply chain management, and customer engagement. By leveraging data analytics, IoT (Internet of Things), and AI (Artificial Intelligence), SKF aims to optimize efficiency, increase productivity, and deliver superior-quality bearings to customers.
1.2 FAG Bearings
FAG has also recognized the importance of digital transformation and has strategically invested in digital technologies to drive its business forward. The company’s digitalization initiatives span across research and development, manufacturing, distribution, and customer support. By embracing Industry 4.0 principles and harnessing data-driven insights, FAG aims to elevate its product quality and customer service.
Product Design and Development
2.1 SKF Bearings
Incorporating digital tools in the product design and development process has enabled SKF to create innovative bearing solutions that meet diverse customer needs. The use of virtual modeling, simulations, and data analytics allows SKF to optimize bearing designs, improve performance, and shorten development cycles. Digital transformation facilitates precision engineering and product customization, resulting in high-quality bearings tailored to specific applications.
2.2 FAG Bearings
Similarly, FAG’s digital product design and development processes have accelerated innovation and improved product quality. By leveraging virtual simulations and prototyping, FAG can efficiently test and validate bearing designs, ensuring that products meet stringent performance criteria. Digitalization enables FAG to deliver cutting-edge solutions with superior reliability and durability.
Manufacturing and Quality Control
3.1 SKF Bearings
Digital transformation has revolutionized SKF’s manufacturing processes, enhancing efficiency and product quality. The integration of smart manufacturing technologies and IoT-enabled sensors enables real-time monitoring of production lines, ensuring consistent and precise manufacturing. This level of digital control improves product uniformity and reduces the risk of defects, enhancing the overall quality of SKF bearings.
3.2 FAG Bearings
FAG’s commitment to digitalization in manufacturing has also yielded significant benefits. IoT-driven data analytics and automation allow FAG to optimize production processes, minimize lead times, and improve quality control. The ability to identify and address potential production issues proactively contributes to the consistent quality of FAG bearings.
Supply Chain Management
4.1 SKF Bearings
Digitalization has streamlined SKF’s supply chain management, enabling efficient inventory management and timely deliveries. Real-time data analytics and AI-powered demand forecasting enhance SKF’s ability to anticipate customer needs and maintain adequate stock levels. The optimized supply chain ensures that customers receive high-quality bearings promptly, boosting customer satisfaction.
4.2 FAG Bearings
FAG’s digital supply chain management processes also contribute to improved product quality and customer service. The integration of digital technologies in logistics and inventory management allows FAG to respond quickly to market demands, ensuring on-time deliveries and minimizing the risk of stockouts.
Customer Engagement and Service
5.1 SKF Bearings
Digital transformation has enhanced SKF’s customer engagement strategies. The company leverages data analytics and AI to gain insights into customer preferences and behavior, enabling personalized customer interactions. Digital platforms, such as online portals and mobile applications, provide customers with easy access to information and support, fostering stronger relationships and customer loyalty.
5.2 FAG Bearings
FAG’s digital customer engagement initiatives prioritize responsive communication and support. Digital channels enable FAG to address customer inquiries promptly and offer technical expertise, enhancing the overall customer experience. Digital transformation has allowed FAG to build enduring relationships with customers and improve customer satisfaction.
Conclusion
In conclusion, digital transformation has significantly impacted the informationization processes of SKF and FAG, shaping their approach to product design, manufacturing, supply chain management, and customer engagement. Both companies have embraced digital technologies to enhance efficiency, optimize processes, and deliver high-quality bearings tailored to customer needs.
Through their ongoing commitment to digital transformation, SKF and FAG can continue to drive innovation, improve product quality, and elevate customer satisfaction in the dynamic and competitive bearing industry.
We support more information about Bearings. you can visit https://cmtgbearing.com. or email us info@cmtgbearing.com.