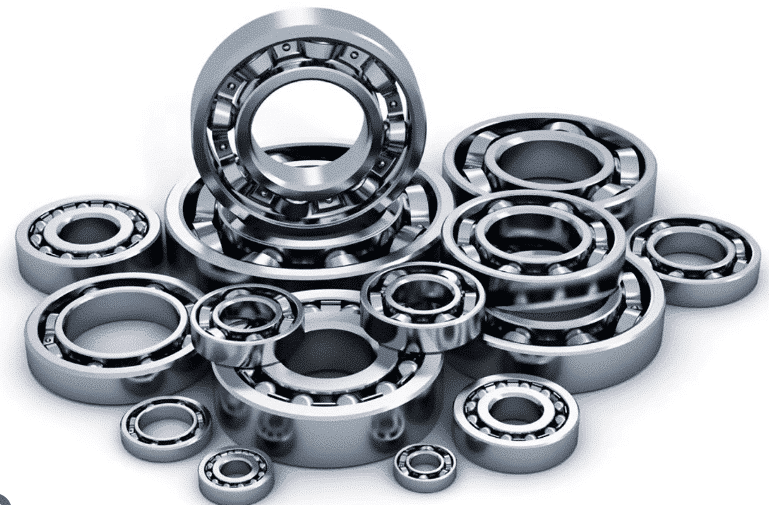
When it comes to industrial machinery and equipment, the total cost of ownership includes not only the initial purchase price but also ongoing maintenance expenses. Bearings, as critical components, greatly influence maintenance costs by impacting factors like durability, longevity, and ease of maintenance. Among the reputable contenders in the bearing market, FAG bearings and TIMKEN bearings have gained recognition for their contributions to reducing maintenance expenses. This article conducts a comprehensive analysis of the maintenance cost aspects associated with FAG bearings and TIMKEN bearings, exploring their unique attributes, advancements, and how they influence the decision-making process.
Durability and Longevity:
One of the primary factors influencing maintenance costs is the durability of bearings. FAG bearings, with their precision engineering and low friction properties, often exhibit extended service life. The minimal tolerances and precise fitting reduce wear and contribute to lower maintenance requirements. This is particularly beneficial in applications where downtime for maintenance is costly, such as manufacturing lines.
TIMKEN bearings, renowned for their rugged design and load-handling capabilities, also contribute to reduced maintenance costs. Their ability to endure harsh conditions and heavy loads leads to longer intervals between maintenance cycles. This is advantageous in industries like construction and mining, where frequent maintenance can lead to substantial operational downtime.
Lubrication and Wear:
Proper lubrication is crucial for bearing longevity. FAG bearings, engineered with precision, require careful lubrication to ensure optimal performance. However, their low friction design reduces the demand for frequent re-lubrication, which can translate to cost savings in terms of labor and lubrication materials.
TIMKEN bearings, with their integrated lubrication solutions and advanced materials, often require less frequent lubrication. This not only saves on maintenance efforts but also reduces the risk of inadequate lubrication causing premature wear.
Ease of Replacement:
The ease of bearing replacement significantly impacts maintenance costs. FAG bearings’ precise fit and standardized dimensions contribute to straightforward replacements, reducing the need for specialized labor and minimizing downtime.
TIMKEN bearings, with their wide availability and extensive distribution network, offer readily accessible replacements, further reducing equipment downtime. This is particularly beneficial in industries where operational continuity is paramount.
Predictive Maintenance:
Both FAG and TIMKEN contribute to predictive maintenance through innovations. FAG’s smart bearings with integrated sensors enable real-time monitoring and early fault detection, facilitating proactive maintenance. TIMKEN’s focus on predictive maintenance solutions helps identify potential issues before they escalate, reducing the likelihood of costly breakdowns.
Conclusion:
The decision between FAG bearings and TIMKEN bearings involves assessing not only initial costs but also long-term maintenance considerations. FAG bearings’ precision engineering and low friction properties lead to reduced wear and optimized lubrication, contributing to lower maintenance expenses. TIMKEN bearings’ durability and load-handling capabilities extend maintenance intervals and facilitate easier replacements. Ultimately, the choice should align with the specific needs of the application, taking into account factors such as industry, operational demands, and maintenance budgets. Both brands offer solutions that contribute to minimizing maintenance costs and enhancing the overall efficiency and reliability of industrial machinery.
We support more information about Bearings. you can visit https://cmtgbearing.com. or email us info@cmtgbearing.com.